The Lean philosophy that was born from the culture of Toyota in the construction of vehicles, has allowed to reach different organizations from different industries by adopting some methods that have been built over many years and that have generated a positive impact, are already part of the DNA of the organization showing results at all levels and became best practices that are used on a daily basis.
One of them is Toyota Kata, paraphrasing the definition in Culture Toyota Kata (2018), by author Mike Rother, indicating that “It is a process to develop competences by creating scientific thinking capacities that are applicable to any objective that represents a challenge , acquiring knowledge through experience and experimentation that are a regular part of daily activities through a small routine of structured practice, between an apprentice and a mentor who become habits and provide new skills through learning ” .
Some say that my teaching is absurd. Others, it is high but not practical. But for those who have seen within themselves, the absurd makes sense. And for those who put it into practice, its height has deep roots.
Lao Tzu, Tao Te King
Roles
The process is a relationship between a mentor who accompanies an apprentice to achieve his or her challenge-driven goals.
Apprentice: main person in charge of the process, defines the what and how, is in charge of executing the actions, understands their challenge by analyzing their environment and experiments to achieve their objectives through learning.
Mentor (coach): responsible for the method, ensures that the apprentice works scientifically according to patterns, offers corrective feedback on their actions and helps the apprentice improve their skills to increase their skills through their experience.
Sometimes another role is added, which is a second coach, who is a person who acts as an observer and gives feedback to the mentor about the accompaniment he is giving to the apprentice.
Routines
TK se estructura con dos rutinas que guían el proceso para comprender el
TK is structured with two routines that guide the process to understand scientific thinking.
Improvement Kata: It is a routine that consists of four steps where good practice habits are defined and taught for the improvement process. In The Toyota Way to Service Excellence (2016), by the author Jeffrey K. Liker who indicates the four parts of the improvement kata:
- Understand the Direction. How do my improvement activities contribute to a broader goal that is important to the organization? Actual state.
- Graspa current Situation. understand current operating patterns in gemba from direct observation and the use of data to better understand what is happening.
- Obstacles and establish next Target Condition. Define the following operational pattern that will bring us closer to the challenge and obstacles that stand between us and the next objective state.
- PDCA towards the Target Condition. This is where the Plan-Do-Check-Act cycle is applied as a series of rapid learning cycles in which predictions are made about what is expected to occur in each experiment after which the prediction results are compared. with the hypothesis.
Coahing Kata: It is a routine of five practice questions for teaching the Kata pattern through dialogue between a mentor and an apprentice in coaching cycles.
It consists of the following questions that the mentor asks the learner:
- What is the target condition?
- What is the actual condition now?
- What obstacles do you think are preventing you from reaching the target condition? Which one are you addressing now?
- What is your next step? What do you expect?
- When can we go and see what we have learnt from taking that step?
Cycle
The Toyota Kata cycle is made up of two parts that the learner must go through with the improvement Kata and the mentor with the coaching Kata where actions are planned and executed.
Planning: This part is focused on understanding the purpose of the challenge, directing the actions to be carried out, identifying opportunities for improvement, understanding the current state and establishing the next objective state. Depending on the agreement of the cadences a deadline is defined, whether they are weekly, monthly, quarterly or annual cadences (depending on the context and the organizational level, whether strategic, tactical or operational).
The definition of the challenge is the point where they connect the strategy and execution, therefore it is important that the challenge is directed by leaders inspired by the strategic objectives of the organization. Historical indicators that allow knowing when the following condition is reached are analyzed.
Execution: Carry out experiments with short durations, the purpose is to carry out actions that take little effort and if large impacts. This is where the experiments and coaching cycles take place, recording the experiments and lessons learned. Execution is the responsibility of the learner, however, you may receive recommendations from the mentor to facilitate the learning cycle.
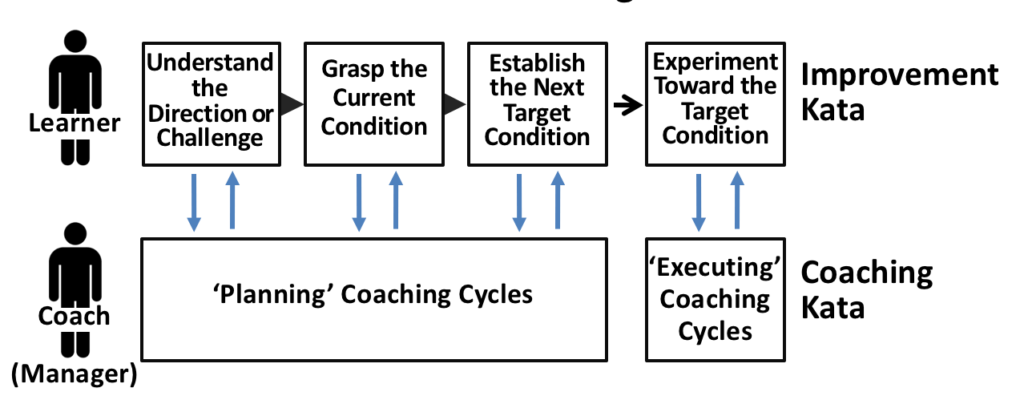
Toyota kata is a method that helps organizations mobilize improvement actions through a mentoring cycle where an expert person teaches the pattern to an apprentice helping him to grow in his skills through learning by experiment.
Sources:
- Toyota Kata Culture: Building Organizational Capability and Mindset through Kata Coaching- Mike Rother
- The Toyota Way to Service Excellence: Lean Transformation in Service Organizations – Jeffrey K. Liker
- https://leanfrontiers.com